Flow sensors are an essential part of the systems that make up our modern way of life. They are at work in your vehicle’s fuel system, gas and water system distribution infrastructures, and countless other manufacturing systems. Several varieties of flow sensors exist, but we’ll focus on the two most famous types of flow sensors and how they work.
What is a Flow sensor
A flow sensor is a component that measures the flow of a fluid such as a gas or liquid. Flow sensors utilize both mechanical and electrical subsystems to measure changes in the fluid’s physical attributes and calculate its flow. Measuring these physical attributes depends on the fluid’s physical attributes. Gaseous, liquid, and non-Newtonian fluids behave vastly different from one another, so the methods we use to measure their flow must be different as well.
Thermal flow sensors are devices used to measure fluid flow based on the principle of heat transfer. These sensors utilize the temperature changes caused by fluid flow to determine the flow rate or velocity. Thermal flow sensors are commonly used in various industries, including the HVAC system, gas and liquid flow monitoring, and industrial process control. The operation of thermal flow sensors is based on the concept that fluid flow carries heat away from a heated element or generates a temperature difference in the heated element. By measuring the resulting temperature change, the flow rate can be determined. The two main types of thermal flow sensors are:
Types of direct current measurement
- Turbine current sensor
- Coriolis sensor
Indirect method
This is the most common method of measuring flow, since direct flow measurement is not possible in most cases. So this method mostly uses an indirect method, the sensor measures the fluid flow indirectly, such as transmitting sound waves through the fluid flow.
Types of measurement of indirect fluid flow
- Differential pressure flow meter
- Inductive magnet
- Frequency of eddies
- Ultrasonic flow meter
- Venturi meter
- Open the disc
- Hold the tube
- Annubar
- Powerful nozzle
- Thermal mass flow meter
- Positive displacement flow meter
What are the types of current sensors? Derivative current sensor
- Differential pressure flow sensor
- Flow rate sensor
- Volume flow sensor
- Mass flow sensor
Derivative current sensor
In this type of flow sensors, flow measurements are made indirectly, for example, the temperature and pressure of the flow are measured to determine the flow rate. Types of inductive current sensors include magnetic sensors, turbine sensors, target sensors, etc. The types of inductive current sensors are as follows:
Turbine current sensor
In this type of flow measurement, a rotor is placed inside the tube and this rotor is supported by two bearings. A magnetic collector is placed at the top of the pipe section where the rotor is mounted. As the fluid flows, the rotor rotates and this creates a frequency. To determine the current speed, the pulsation of the rotor is counted.
Turbine Flow Meter
Advantages of turbine flow sensors
- Easy installation
- Not affected by density fluctuations
- Compact
- Less head loss
- Good temperature and pressure rating
- Good repeatability and range
Disadvantages of turbine flow sensors
- Cannot be used with very viscous liquids
- Due to moving parts, damage can occur when the speed increases
- Turbine Flow Sensor Applications
- Military applications
- Oil industry
- Measurement of fuel energy and cryogenic flow
Target current sensor
In a target flow sensor, an obstacle is placed in the flow path so that when the liquid contacts the target, a force is applied to the target. This force can be measured and that measured force is proportional to the flow rate. The size of the object varies depending on the liquid being measured.
Target Flow Meter
Advantages of the target current sensor
- This flow meter can be used with liquid suspensions
- Can be used to measure flow with low turbulence
Applications of target flow sensors
- Can be used to measure dirty liquids
- It is possible to measure liquid, vapor and gas
Mass flow sensor
Fluid mass is measured directly in this type of flow measurement. These sensors measure the mass or amount of liquid flowing through a pipe to determine the flow rate. Coriolis and thermal mass flow sensors are examples of mass flow sensors. Here are the types of mass flow sensors:
Coriolis mass flow sensor
The principle of operation of this flow sensor is based on Newton’s second law, which states that force equals mass times acceleration. In this meter, the current is divided into two parallel tubes and these tubes are vibrated by an electromagnetic driving coil.
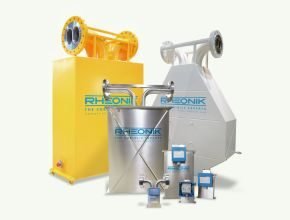
So when the fluid flows through these tubes there will be upward and downward forces and therefore there will be deflection of the tubes and this deflection is known as the Coriolis effect. The deflection of the tube corresponds to the mass flow inside the tube.
Advantages of Coriolis flow sensors
- High accuracy
- Very low pressure drop
- Can be used for both liquid and gas flow
Disadvantages of Coriolis flow sensors
- Expensive
- Installation is difficult
Applications of Coriolis flow sensor
- Natural gas consumption measurement
- Custody transfer
- Syrup and oil monitoring
- Gas & liquid flow measurement
- Solid content concentration can be determined
Thermal Mass Flow Sensor
In this type of sensor, flow measurement is carried out by utilizing the thermal properties of the fluid. In this sensor, a certain amount of heat will be given to the heater located inside the sensor.
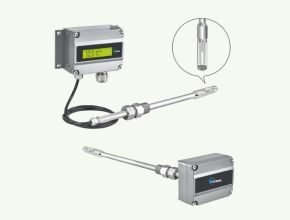
So when the liquid flows, some heat is lost, and increasing the flow also increases the heat loss. This heat loss is measured by a temperature sensor measuring device.
Advantages of thermal mass flow meters
- Measurements are not affected by pressure fluctuations
- Very low pressure drop
- Less maintenance because there are no moving parts
- Installation is very easy
- Economic
Limitations of thermal mass flow meters
- Humidity affects measurements
- Less sensitivity to high current
- If there are differences in gas composition, it must be recalibrated
Accuracy is reduced due to stacking of flow sensors
- Applications of thermal mass flow sensors
- Measurement of gases such as nitrogen, hydrogen, helium
- Pure gas measurement
Differential pressure flow sensor
In this type of flow sensor, the flow pressure difference resulting from the tube structure is used to determine the flow rate. Here are the types of differential pressure flow sensors:
Venturi flow meter
This type of sensor is a tube with a conical structure. The operation of the differential pressure flow meter is based on Bernoulli’s principle, according to which when the velocity of the liquid increases, the pressure decreases and vice versa.
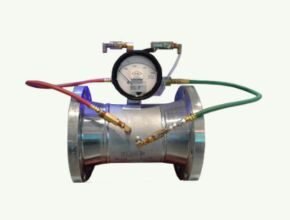
The structure of the tube is such that there are converging sections as well as diverging sections. So when the fluid flows through the converging part of the tube it gets accelerated and during this process, the pressure of the fluid goes down. The final part of the tube section is expanded and at this section, the fluid flow almost gets the actual pressure. So the relationship of velocity and pressure is examined and according to this, we can determine the flow rate.
Advantages of venturi meter
- Good accuracy
- High speed and pressure recovery
- Can be used with liquids containing small solids
- High repeatability
- Less maintenance
Disadvantages of venturi meters
- High installation costs
- Abrasive or sticky liquids will affect the measurement
Applications of venturi meter
- Measurement of compressible and incompressible fluids
- Measurement of flow of gas and liquid
- Chemical industry
- Oil and gas
- Electrical industry
- Nozzle plateThis type of flow sensor has a plate-like design and is installed in the direct path of the pipe. The nozzle is installed perpendicular to the fluid flow. There is a hole in the center of this plate, so when the liquid comes in contact with the plate, the liquid flows through the hole and the flow rate increases and the pressure decreases.
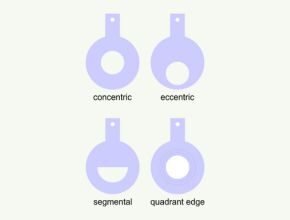
So when the fluid flows outside the orifice plate, the flow velocity and pressure will change. The relationship between pressure drop and velocity can be observed to determine the flow rate.
Advantages of orifice plates
- Economical
- Easy to maintain
- Generates high differential pressure
- Can be easily replaced
- No moving parts
- High accuracy
Disadvantages of orifice plates
- High permanent pressure loss
- Cannot be used with dirty liquids
- Frequent calibration required
- Measurements are affected due to variations in density, viscosity, etc.
Applications of orifice plates
- Neutral gas transfer
- Gas and liquid measurement
- Purification
- Oil and gas
Pitot Tube
A pitot tube can be considered as a probe that has two parts and is capable of sensing both static and dynamic pressure. This type of flow sensor is used for non-uniform flow measurement, so due to non-uniform flow, there will be variations in pressure and flow velocity. The probe will be inserted into the fluid, the impact unit of this flow meter consists of a tube with one end bent at a right angle to the direction of flow. The static part of the tube end will be closed but will have a small slot that can be seen on the side of the unit.
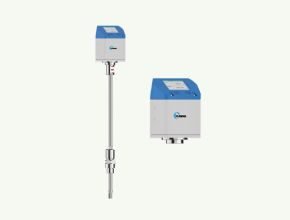
Static pressure will be measured on the flow channel wall and dynamic pressure or impact pressure is calculated from the flowing pressure. The velocity head will be converted to impact pressure. Flow measurement is done by measuring the difference between static and dynamic pressure. Most of these tubes are installed by welding couplings on the pipe and after that, the probe will be inserted through the coupling.
Advantages of Pitot tubes
- Easy installation
- No pressure loss
Disadvantages of Pitot tubes
- Cannot be used with dirty liquids
- Not suitable for measuring sticky liquids
- Sensitive to disturbances upstream
- Low accuracy
Applications
- Can be used to measure non-uniform flow
- Velocity and direction measurement in combustion studies and in heat transfer work
- It is used to determine the magnitude and direction of gas velocity
- Aircraft airspeed measurement
Annubar Flow Meter
The operation of the Annubar is similar to that of the Pitot tube. The only difference is that the Annubar has more than one hole in the pressure measuring chamber. So, this device has multiple velocity sensing holes that are exposed to the fluid flow. So from here, static and dynamic pressures are calculated and the difference between the two can be calculated to determine the fluid flow.
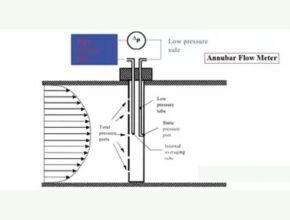
Advantages of Annubar
- Easy installation
- Low pressure drop
- Low maintenance
- High accuracy
Disadvantages of Annubar
- Cannot be used with high viscous liquids
- Measurement is a single point
Annubar Applications
- Used for liquid and gas flow
- Can be used for both low and high pressure applications
Flow Nozzle
This is another type of differential pressure flow sensor and can handle higher flow rates than orifice plates. This type of flow meter is similar to a venturi but there is no recovery cone. Basically a flow nozzle is a fluid flow restrictor and has a cylindrical throat section.

A pressure tap is required to measure the static pressure difference created by the flow nozzle, and will be located, upstream and downstream in the pipeline. This type of flow meter can be used to determine the flow of liquids with suspended solids. The cost and size of this meter is very less, the pressure loss of this meter is very high. This type of flow meter is used when high velocity and pressure recovery is required.
Advantages of the flow nozzle
- Can be used to detect high flow
- Measurement of liquids with solid particles is possible
- Low pressure drop than orifice plate
Disadvantages of the flow nozzle
- Cannot be used with viscous liquids
- Should not be used with liquids that have sticky particles
- More maintenance
- Cannot be used with large size pipes
Applications of flow nozzles
- High pressure steam flow
- High temperature vapor flow
- Mostly used for gas rather than liquid measurement
- It is used with pressure transmitters
- It is used with flow control valves
Velocity Flow Sensor
This type of flow sensor will measure the velocity of flow through the pipe. So the speed of the fluid will be multiplied by the area through which the fluid passes. Here are the types of velocity flow meters:
Magnetic Flow Sensor
In this type of flow sensor, a magnetic field will be applied to the pipe or channel whose flow will be measured. The operating principle of this flow sensor is based on Faraday’s law, which states that when a conductive fluid passes through a magnetic flux, a GGL will be created. So when a conductive fluid passes through a magnetic field, a voltage will arise. The voltage formed will be proportional to the flow velocity.
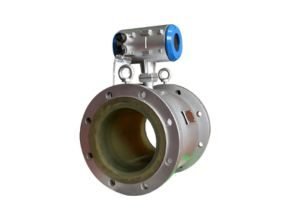
Advantages of magnetic flow sensors
- Has no moving parts and also no liquid obstruction
- Very little pressure drop
- Non-contact measurement
- Good electrical insulation and corrosion resistance
- Can be used with very low flows
- Can be used for bi-directional flow measurement
- Measurement will not be affected by viscosity
Disadvantages of magnetic flow sensors
- Only conductive liquids can be measured, we will not be able to measure gases and hydrocarbons with these
- Relatively expensive price
Applications of magnetic flow sensors
- Measurement of slurries and dirty liquids can be done
- Can be used with acids, bases, water, and also for aqueous solutions
Vortex Flow Sensor
In this type of flow measurement, a barrier will be placed perpendicular to the flow. When the fluid passes through the barrier, the flow will be disrupted and a vortex will form.
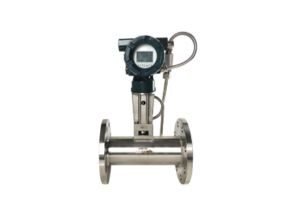
The frequency of this vortex shedding can be used to determine the velocity of the fluid. Most pressure transducers are used to measure vortices.
Advantages of vortex flow sensors
- High accuracy
- No moving parts so less maintenance
- Can be used with liquids, gases, and vapors
- Very low pressure drop
- Can be used with liquids of different densities
Disadvantages of vortex flow sensors
- Cannot be used with rough or dirty liquids
- Measurements will be affected if the flow velocity is low
- To create proper vorticity, a defined straight pipe path is required for upstream and downstream of the sensor
Applications of vortex flow sensors
- Cryogenic liquids
- Hot and cold water
- Condensate measurement
- Acids
- Solvents
- Vapor measurement
Volumetric Flow Sensor
Flow measurement will be carried out by measuring the volume of fluid flowing through the pipe. Here are some types that use the volumetric flow sensor method:
Positive Displacemenet Flow Sensor
This type of flow sensor is used for gas and liquid measurement. There are several types of positive displacement sensors such as rotating paddle sensors, oscillating piston sensors, oval gear sensors, sliding vane sensors, and bi rotor sensors.
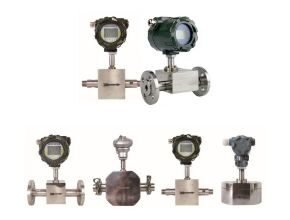
Most positive displacement sensors have moving parts, the mechanical components of the PD sensor are driven due to energy from the flow. The energy that moves the sensor will create a pressure drop at the inlet and outlet of the meter.
Advantages of positive displacement flow sensors
- Can be used with viscous liquids
- Certain types of PD meters do not require electrical power for operation
- Good coverage power
Disadvantages of positive displacement sensors
- Cannot be used with liquids that have suspended particles
- Possibility of high mechanical wear due to moving parts
- Excessive speed may damage the sensor
Applications of positive displacement flow sensors
- Measurement of very low and very high viscous liquids
Ultrasonic Flow Sensor
In this type of flow sensor, sound waves will be used to determine the flow rate. There are three measurement methods in this type of sensor, namely the Doppler shift method, the deflecting beam method, and the transit time method.
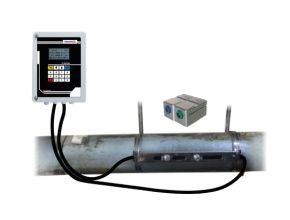
In the image above, we can see two transducers placed in opposite directions. These two transducers will emit sound waves to each other and the time taken to receive both signals is measured to determine the velocity of the fluid.
Doppler shift method
In this method, sound waves will be transmitted through the fluid and these waves will be reflected from the fluid to the receiver in the flow sensor. The frequency of the received sound waves can be measured to determine the flow rate.
Deflecting beam method
In this method, the sound waves are transmitted at a right angle to the flow. The fluid will deflect the sound waves. This deflection can be measured to determine the flow rate.
Flow transit time
In this method, a diagonal beam will be transmitted across the flow path and this beam will be transmitted against the flow. The sound traveling against the flow will be slow and this can be measured to determine the flow rate.
Advantages of ultrasonic flow sensors
- Non-intrusive
- No pressure drop
- Good accuracy
- Good range
- High reliability
Limitations of ultrasonic flow sensors
- Cannot be used with dirty liquids
- A straight tube is needed to measure the current
- Weakening affects transmission lines
How to choose a current sensor for our application? It must be chosen according to the type of liquid, such as clean or dirty
- Fluid properties such as pressure, density, viscosity, conductivity, temperature, pressure drop, etc.
- It should be selected according to factory conditions such as pipe size, straight pipe, cap, etc.
- The flow sensor must be selected according to the required performance, such as accuracy, repeatability, stability and according to the pressure drop.
- Area requirements
- Installation mode
- It should be chosen taking into account the current, for example if it contains corrosive or corrosive materials
- What can be the main causes of flow meter errors? This can be caused by variations in fluid properties such as density, viscosity, pressure and temperature
- Direction of meter
- Power failure
- Conclusion
The following conclusions can be drawn from the article “Definition, Types and Differences of Current Sensors” described above:
Flow sensors are components that measure the flow of fluids such as gas or liquid. Flow sensors use mechanical and electrical subsystems to measure changes in the physical properties of a fluid and calculate its flow. There are two methods of measuring flow namely direct and indirect. Direct current measurement is carried out: in turbine flow sensor and Coriolis sensor
Indirect flow measurement has been applied: differential pressure flowmeter, magnetic-induction, swirl frequency, ultrasonic flowmeter, venturi meter, nozzle, pitot tube,
Annubar, flow nozzle, thermal mass flow meter and shear flow meter. There are 5 types of flow sensors namely: induction flow sensor, differential pressure flow sensor, velocity sensor, volume flow sensor and mass flow sensor.
Flow sensors are vital components in various systems, ranging from vehicle fuel systems to large-scale industrial processes. They measure the flow of fluids, which can be gases or liquids, using both mechanical and electrical subsystems. The choice of flow sensor depends on the specific properties of the fluid being measured and the application requirements. There are two primary methods for measuring flow: direct and indirect. Direct methods include turbine and Coriolis sensors, while indirect methods encompass a variety of techniques such as differential pressure, ultrasonic, and magnetic-induction flow meters. The main types of flow sensors are induction flow sensors, differential pressure flow sensors, velocity sensors, volume flow sensors, and mass flow sensors.
Conclusion
Flow sensors are vital components in various systems, ranging from vehicle fuel systems to large-scale industrial processes. They measure the flow of fluids, which can be gases or liquids, using both mechanical and electrical subsystems. The choice of flow sensor depends on the specific properties of the fluid being measured and the application requirements. There are two primary methods for measuring flow: direct and indirect. Direct methods include turbine and Coriolis sensors, while indirect methods encompass a variety of techniques such as differential pressure, ultrasonic, and magnetic-induction flow meters. The main types of flow sensors are induction flow sensors, differential pressure flow sensors, velocity sensors, volume flow sensors, and mass flow sensors.
FAQ
Q1: What is a flow sensor? A1: A flow sensor measures the flow of a fluid, such as a gas or liquid, by using mechanical and electrical subsystems to detect changes in the fluid’s physical attributes.
Q2: What are the primary methods of measuring fluid flow? A2: The two primary methods are direct and indirect flow measurement. Direct measurement includes methods like turbine and Coriolis sensors, while indirect measurement includes techniques such as differential pressure, ultrasonic, and magnetic-induction flow meters.
Q3: What are the main types of flow sensors? A3: The main types are:
- Induction flow sensors
- Differential pressure flow sensors
- Velocity flow sensors
- Volume flow sensors
- Mass flow sensors
Q4: How do thermal flow sensors work? A4: Thermal flow sensors measure fluid flow based on the principle of heat transfer. They detect temperature changes caused by fluid flow to determine the flow rate or velocity.
Q5: What are the advantages of turbine flow sensors? A5: Advantages include easy installation, not being affected by density fluctuations, compact size, low head loss, good temperature and pressure ratings, and good repeatability and range.
Q6: What are the disadvantages of turbine flow sensors? A6: Disadvantages include being unsuitable for very viscous liquids and the potential for damage due to moving parts when flow speed increases.
Q7: How do Coriolis mass flow sensors operate? A7: Coriolis mass flow sensors operate based on Newton’s second law, where force equals mass times acceleration. Fluid flow through vibrating tubes causes deflection, which is measured to determine the mass flow rate.
Q8: What are the advantages and disadvantages of Coriolis flow sensors? A8: Advantages include high accuracy, very low pressure drop, and suitability for both liquid and gas flow. Disadvantages include high cost and difficult installation.
Q9: What factors should be considered when choosing a flow sensor? A9: Factors to consider include the type of liquid (clean or dirty), fluid properties (pressure, density, viscosity, conductivity, temperature), installation conditions (pipe size, straight pipe requirements), required performance (accuracy, repeatability, stability), and compatibility with corrosive materials.
Q10: What are common causes of flow meter errors? A10: Common causes include variations in fluid properties (density, viscosity, pressure, temperature), incorrect meter orientation, and power failures.
Refference :
https://automationforum.co/
https://www.blue-white.com/article/flow-meter-types-their-functions/